The Difference Between The Cast, Forged and Billet Processes
If you’ve researched getting your product or part manufactured, you’ll probably have come across the terms Cast, Forged and Billet. It’s not always easy to find information about what these mean or the pros and cons of each process. So we’re going to take you through the processes involved in each, and help you make an informed decision.
Let's define our terms.
Cast
Cast metal has been heated up and poured into a mould. These casting techniques include gravity or high pressure die casting. This forms the shape of your product.
Forged
Forged metal is heated until it is malleable (not molten) and pressed or forced into the desired shape. This how blacksmiths made horseshoes, swords and armour. Modern methods use high pressure stamping, rather than a hammer and anvil.
Billet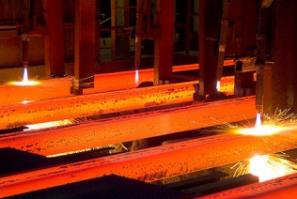
Billet is a type of metal and doesn’t necessarily represent the manufacturing process (or quality) of the final product. Billet metal is a solid length that has been rolled or cast into shape. Billet material is often used in machining.
Which is better for ME?
Each process has its pros and cons depending on the project constraints. These could be budget, product size, manufacturing quantity, tolerances or type of finish. Casting is highly versatile and can cater for smaller orders with processes such as sand casting, or bulk orders with processes such as high-pressure die casting. Casting is a ‘near-net-shape’ forming method, so there's minimal waste, and there's virtually no post-processing required to form the component's shape The materials are easy to work with, and a wide variety of surface finishes can be applied.
Forging a part results in high strength, high quality units but the downside is that it requires extensive finishing work. Forging is limited to simpler shapes, free from overhangs or too many concave surfaces.
Billet material, however, is not a manufacturing process, it's just a type of metal and is often used for CNC machining products, producing high quality, accurate parts without the need for expensive tooling. This makes it great for low quantity or bespoke work.
While CNC machining of billet material is possible for large scale production; the cost increases with each unit.
While other processes are available, we believe the versatility of casting, combined with robust design and advanced CNC methods will serve the majority of needs.
To learn more about our casting journey, check out our infographic or contact us today to speak to one of our casting experts.
Contact us today to find out how we can support you with your next project.
HOW can MRT Castings help you?
I want...
- Select what you need
- a complete solution
- to develop a new component from initial concept
- advice on what processes are best suited to my component
- prototypes before committing to production tooling
- to re-shore production to the UK from overseas
- a new supplier to use existing tooling
- to convert a machined from solid part to a casting
- a supplier who can meet stringent quality requirements